Ausfallzeiten – Definition, Ursachen und Auswirkungen
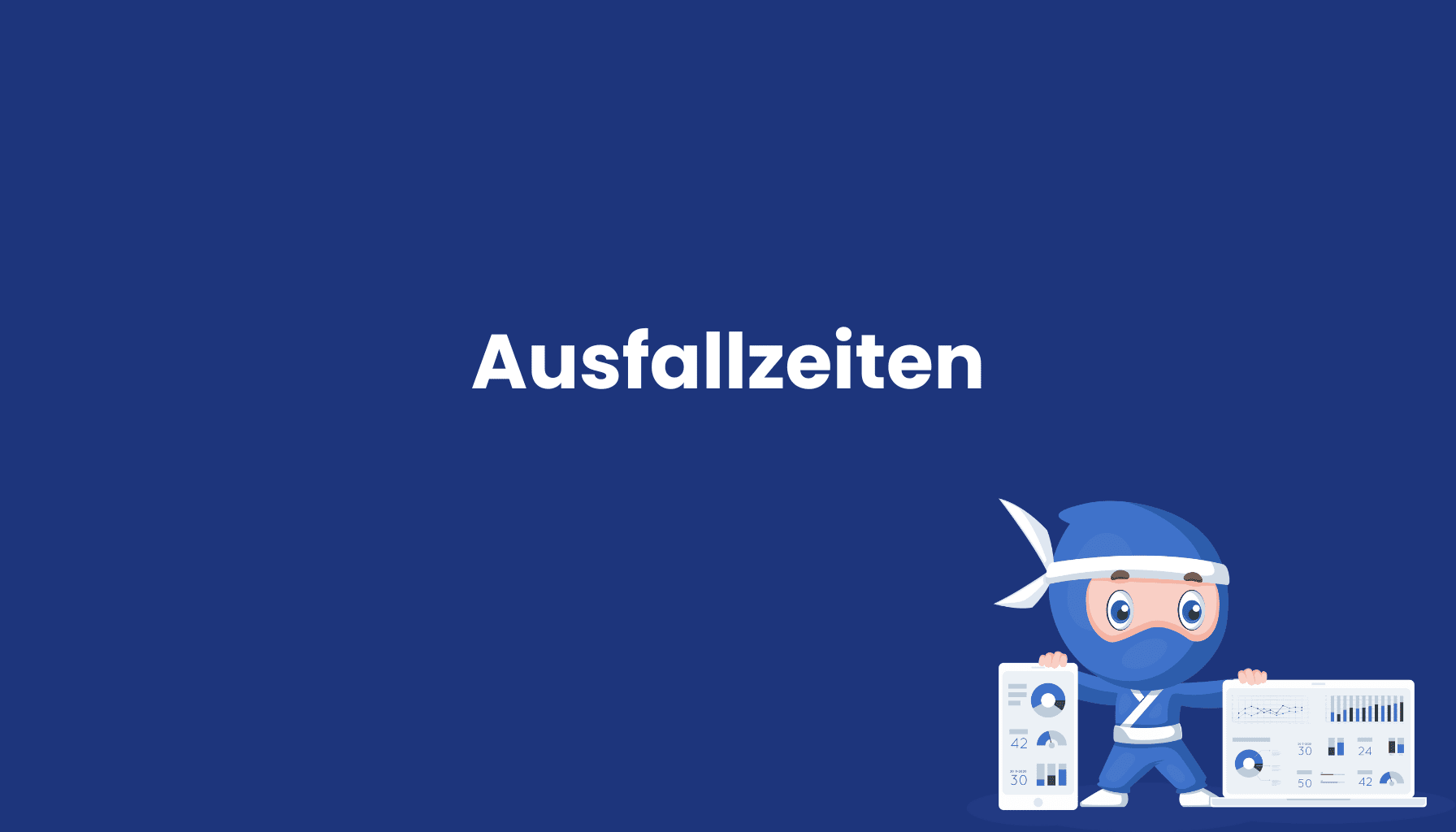
Was sind Ausfallzeiten?
Ausfallzeiten, auch als Stillstandszeiten bezeichnet, sind Zeiträume, in denen Produktionsanlagen oder Maschinen nicht in Betrieb sind und keine wertschöpfenden Tätigkeiten ausgeführt werden. Diese Unterbrechungen können geplante Wartungsarbeiten, ungeplante Maschinenstörungen oder externe Faktoren wie Lieferengpässe umfassen.
Ausfallzeiten haben einen direkten Einfluss auf die Effizienz und Produktivität eines Unternehmens und können zu erheblichen finanziellen Verlusten führen.
Ursachen für Ausfallzeiten
Geplante Wartungsarbeiten:
Geplante Ausfallzeiten sind notwendig, um Maschinen zu warten, zu inspizieren und zu reparieren. Diese Art von Stillstand kann durch präventive Wartungsstrategien minimiert werden, um die Maschinenverfügbarkeit zu maximieren.
Ungeplante Störungen:
Ungeplante Ausfallzeiten treten aufgrund von Maschinenfehlern, Materialmangel, menschlichen Fehlern oder anderen unvorhergesehenen Ereignissen auf. Diese Art von Stillstand ist oft schwer vorherzusagen und kann zu erheblichen Produktionsverzögerungen führen.
Externe Faktoren:
Lieferengpässe, Stromausfälle oder Naturkatastrophen können ebenfalls zu Ausfallzeiten führen. Obwohl diese Faktoren oft außerhalb der Kontrolle des Unternehmens liegen, können sie erhebliche Auswirkungen auf die Produktionsprozesse haben.
Auswirkungen von Ausfallzeiten auf die Produktion
Produktionsverluste:
Jede Minute, die eine Maschine stillsteht, bedeutet verlorene Produktionszeit, was zu einer geringeren Stückzahl und damit zu einem direkten Umsatzverlust führt.
Kostenerhöhung:
Ausfallzeiten führen zu erhöhten Produktionskosten, da fixierte Kosten weiterlaufen, ohne dass wertschöpfende Aktivitäten stattfinden. Zudem können zusätzliche Kosten für Reparaturen, Überstunden und Expresstransporte anfallen.
Qualitätsprobleme:
Wenn Maschinen nicht regelmäßig gewartet werden, kann dies zu einer Verschlechterung der Produktqualität führen, was wiederum Nacharbeit oder Ausschuss zur Folge haben kann.
Ausfallzeiten und ihre Bedeutung für die Overall Equipment Effectiveness (OEE)
Ausfallzeiten sind ein kritischer Faktor für die Berechnung der Overall Equipment Effectiveness (OEE). Die Verfügbarkeit, einer der drei Kernaspekte der OEE, wird direkt durch Ausfallzeiten beeinflusst. Jede Minute Stillstand reduziert die Verfügbarkeit und senkt damit die Gesamtanlageneffektivität. Durch die Analyse der Ausfallzeiten und deren Ursachen können Unternehmen gezielt Maßnahmen ergreifen, um diese Zeiten zu reduzieren und somit ihre OEE zu verbessern. Dies führt zu einer höheren Produktionseffizienz, geringeren Kosten und einer besseren Auslastung der Maschinen.
Strategien zur Reduzierung von Ausfallzeiten
Präventive Wartung:
Regelmäßige und geplante Wartungsarbeiten können Maschinenstörungen vorbeugen und ungeplante Ausfallzeiten minimieren.
Echtzeit-Monitoring:
Durch den Einsatz von Echtzeit-Datenüberwachung können potenzielle Probleme frühzeitig erkannt und behoben werden, bevor sie zu einem Stillstand führen.
Schulung der Mitarbeiter:
Gut geschulte Mitarbeiter können schneller auf Störungen reagieren und so die Dauer von Ausfallzeiten verkürzen.
Fazit
Ausfallzeiten sind ein bedeutender Faktor, der die Effizienz und Rentabilität eines Unternehmens beeinträchtigen kann. Durch gezielte Maßnahmen zur Reduzierung von Ausfallzeiten, wie präventive Wartung und Echtzeit-Monitoring, können Unternehmen ihre OEE verbessern und ihre Produktionskosten senken. Eine proaktive Herangehensweise an das Management von Ausfallzeiten ist daher entscheidend für den langfristigen Erfolg und die Wettbewerbsfähigkeit eines Unternehmens.
Exklusives Whitepaper
Lernen Sie die modernsten Ansätze der Industrie 4.0, die Sie in Ihrer Produktion schon morgen umsetzen können, um innerhalb von 4 Wochen Ihre Kosten um gut 20% zu reduzieren.
mehr erfahren