Was bedeutet OEE? - Definition, Faktoren und Berechnung + Beispiele
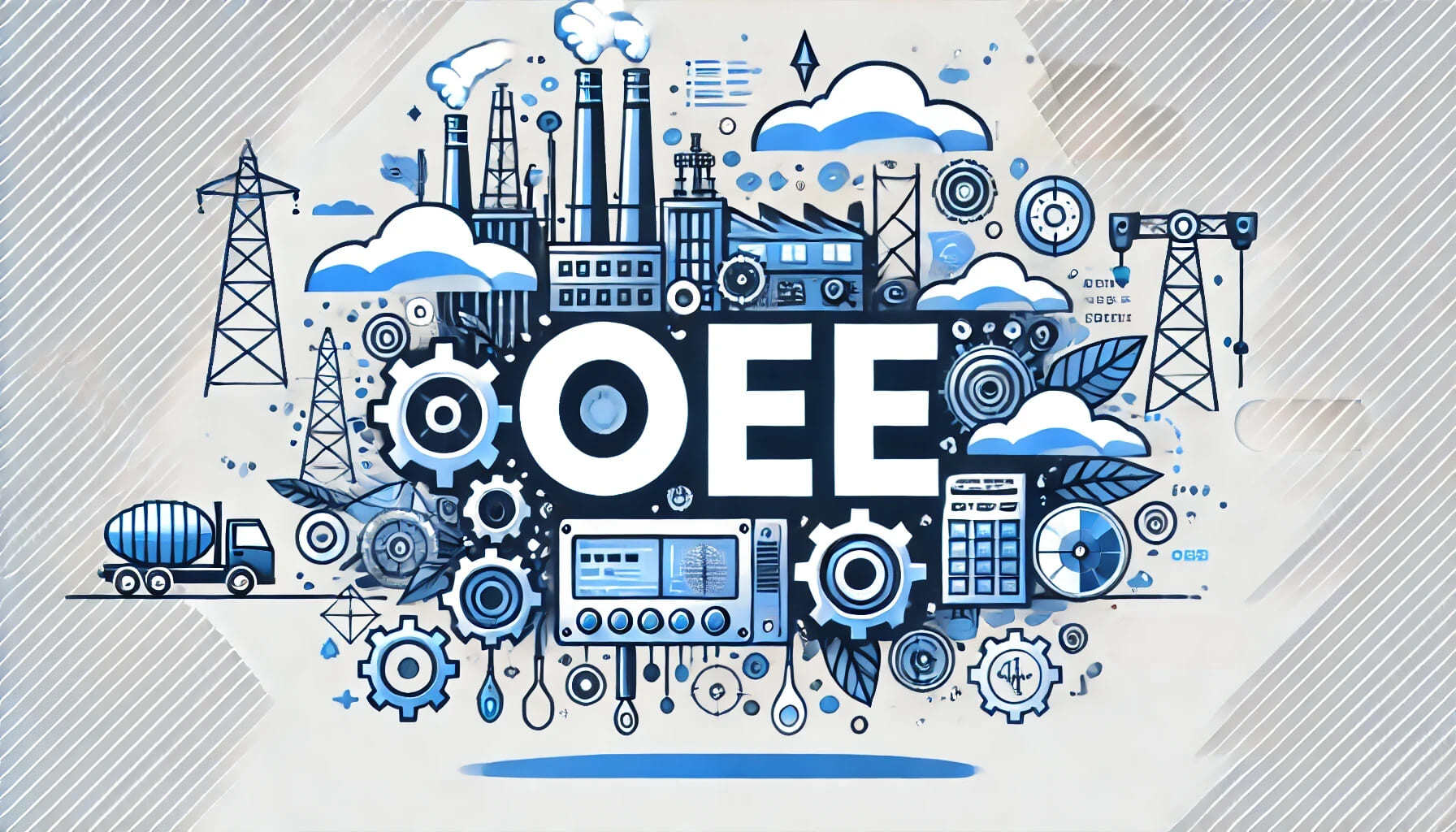
Wir vermitteln Ihnen mit unserem Blog-Artikel das grundlegende OEE Know-how, führen in die OEE Kennzahl und OEE Faktoren an Hand von Beispielen ein und zeigen Ihnen, mit welchen Strategien sie eine OEE Optimierung und Steigerung der Produktivität erzielen.
- Was ist OEE?
- OEE Faktoren und deren Berechnung mit Beispielen
- OEE Formel - Berechnung der Kennzahl
- OEE Fazit
Was ist OEE (Overall Equipment Effectiveness)?
OEE ist die wichtigste Produktionskennzahl zur Messung der Gesamtanlageneffektivität. Sie zeigt in Prozent (0-100%), wie effizient Produktionsanlagen arbeiten:
-
Verfügbarkeit: Wie lange läuft die Anlage?
-
Leistung: Wie schnell produziert die Anlage?
- Qualität: Wie viele Gutteile werden produziert?
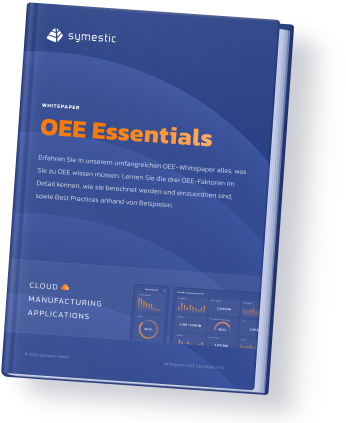
OEE Faktoren und deren Berechnung mit Beispielen
1. OEE - Verfügbarkeitsfaktor
Definition und Formel sowie die Ermittlung der Verfügbarkeitsfaktoren in der Praxis
Die Verfügbarkeit ist die Zeit, in der Ihre Maschine tatsächlich arbeitet, als Prozentsatz der geplanten Arbeitszeit.
Um die Verfügbarkeit zu berechnen, wird die tatsächliche Arbeitszeit durch die gesamte geplante Arbeitszeit dividiert, um den Anteil zu ermitteln, und mit 100 multipliziert, um den Wert in Prozent zu erhalten:
Die geplante Arbeitszeit einer Anlage ist Ihnen aus dem Produktionsplan bekannt. Aber wie ermitteln Sie die tatsächliche Arbeitszeit? Dazu registrieren Sie alle Stillstände (Ausfallzeiten) und subtrahieren sie von allen geplanten Arbeitszeiten.
Aus der Analyse der Stillstands-Daten erkennen Sie neben der Ursache auch das Potential an Verbesserungen. Hierbei lassen sich technische und organisatorische Stillstands-Gründe prinzipiell voneinander unterscheiden.
Beispiel zur Berechnung des OEE Verfügbarkeitsfaktors
In der Praxis ist oftmals die Steigerung der Verfügbarkeit die erste und effektivste Maßnahme, um die Overall Equipment Effectiveness (OEE) rasch zu verbessern. Durch eine automatische Messung der Verfügbarkeit bzw. Stillsände werden Sie rasch erkennen, wie stark Betriebszeit und Produktionszeit einer Anlage voneinander abweichen.
Strategie zur Optimierung der Verfügbarkeit
Sie können in der Praxis nur im Rahmen einer automatischen Stillstandserkennung ermitteln, welche Auswirkung die Vielzahl, der über den Tag verteilten Micro-Stillstände in der Summe haben. Auch der Einfluss der Rüstzeiten auf die Gesamtverfügbarkeit einer Anlage wird so schnell ersichtlich. Dies kann in Ihrer Produktionsplanung nachvollzogen und zukünftig dann besser berücksichtigt werden.
Ermitteln Sie also automatisiert den IST-Zustand der Verfügbarkeit bzw. Stillstände Ihrer Anlagen und Maschinen sowie die Ursachen, die hierzu geführt haben und lassen Sie sich das in einem Produktionskennzahlen-Dashboard für OEE, Stillstände etc. visualisieren. Dies gelingt Ihnen schnell, einfach und kosteneffizient durch den Einsatz eines auf OEE und weitere Produktionskennzahlen spezialisierten Software-as-a-Service (SaaS) Tools.
In der Regel zeigt sich, dass der Großteil der Stillstände aus einer Handvoll Gründe erfolgt. Diese können je nach Anlage und Prozess sehr unterschiedlich sein, aber meist ergeben Auswertungen einige wenige „Hauptschuldige“. Wie so oft gilt meist auch hier das Pareto-Prinzip:
-> 20 % der Gründe führen zu 80 % der Stillstandszeiten.
Achten Sie auf die Einfachheit der Konnektivität bei der Anlagen- und Maschinen-Anbindung. Idealerweise ist das auch in Eigenregie durch Ihre Instandhaltung/Elektriker pro Anlage innerhalb von einer Stunde machbar. Um nicht unnötig Ihre interne IT-Abteilung zu belasten, Störungen mit Ihrem IT-Netzwerk auszuschließen und Cyber-Security Gefahren zu vermeiden, können Sie auch moderne IoT-Edge-Devices mit Mobilfunk einsetzen.
2. OEE - Leistungsfaktor
Definition und Formel sowie die Ermittlung des OEE Leistungsfaktors in der Praxis
Der Leistungsfaktor ist ein Maß für die Produktionsgeschwindigkeit einer Maschine im Vergleich zur idealen Produktionsgeschwindigkeit. Er bewertet, wie effektiv die Maschine im gegebenen Betriebszeitraum arbeitet, indem er die tatsächlich erreichte Produktionsrate mit der theoretisch möglichen maximalen Produktionsrate vergleicht.
Ein optimaler OEE Leistungsfaktor bedeutet, dass die Maschine so schnell wie möglich arbeitet, ohne Einbußen in der Qualität oder unerwartete Unterbrechungen. Die Formel zur Berechnung des Leistungsfaktors lautet:
Ideale Zykluszeit
Die ideale Zykluszeit ist die minimale Zeit, die benötigt wird, um ein Teil unter optimalen Bedingungen zu produzieren.
Anzahl produzierter Teile
Die Anzahl der produzierten Teile ist die tatsächliche Anzahl der Teile, die während der Betriebszeit hergestellt wurden.
Betriebszeit
Die Betriebszeit ist die Zeit, während der die Maschine tatsächlich in Betrieb war.
Ein OEE Leistungsfaktor von 100 % zeigt an, dass die Maschine mit ihrer maximal möglichen Geschwindigkeit arbeitet. Werte unter 100 % weisen auf Effizienzverluste hin, die durch verschiedene Faktoren wie suboptimale Prozesse, Maschinenprobleme oder Bedienfehler verursacht werden können.
Ein OEE Leistungsfaktor von über 100 % sollte jedoch kritisch überprüft werden, um sicherzustellen, dass die ideale Zykluszeit korrekt definiert ist und dass die tatsächlichen Bedingungen des Produktionsprozesses realistisch und nachhaltig sind. Andernfalls könnte ein solcher Wert falsche Erwartungen wecken und potenziell auf versteckte Probleme oder Fehlkalkulationen hinweisen.
Was bei einem OEE Leistungsfaktor von über 100% zu bedenken ist!
Ein Leistungsfaktor von über 100 % deutet darauf hin, dass die Anlage, Maschine oder der Produktionsprozess schneller arbeitet als die ursprünglich angenommene ideale Zykluszeit. Dies kann verschiedene Gründe haben:
- Unrealistisch konservative Zykluszeit
- Optimierung und Verbesserungen
- Abweichung bei der Erfassung der Zykluszeit
- Kurze Produktionsläufe oder spezielle Bedingungen
Wie ermitteln Sie Ihre maximale Produktionsleistung (Soll-Leistung)?
Beispiel zur Berechnung des OEE Leistungsfaktors
wenn in einen Zyklus zwei Teile bearbeitet werden und die ideale Zykluszeit 5 Sekunden beträgt, dann sollten innerhalb einer Minute 24 Teile bearbeitet werden bzw. innerhalb einer Stunde sollten 1440 Teile bearbeitet werden.
Sollte diese Angabe nicht verfügbar sein, dann können Sie die schnellste aufgezeichnete Zeit ermitteln, indem Sie die historische Leistung betrachten und dann berechnen, wie viele Produkte Sie herstellen würden, wenn Ihre Maschinen ständig mit dieser Geschwindigkeit laufen würden.
Strategie zur Optimierung der OEE Leistung
Wie beim Thema der Verfügbarkeit einer Anlage gilt auch beim Leistungsfaktor, dass Sie automatisiert den IST-Zustand der Leistung Ihrer Anlagen und Maschinen erfassen sollten. Dies gelingt auch in diesem Fall schnell, einfach und kosteneffizient durch den Einsatz eines auf Produktionskennzahlen spezialisierten Software-as-a-Service (SaaS) Tools.
Zur Erinnerung: Achten Sie auf die Einfachheit der Konnektivität bei der Anlagen- und Maschinen-Anbindung. Idealerweise sogar in Eigenregie durch Ihre Instandhaltung/Elektriker. Pro Anlage ist das in der Regel innerhalb von einer Stunde machbar.
Die Vorgehensweise ist analog zur Ermittlung und Analyse der Verfügbarkeit, so dass wir uns dieser Stelle nur kurz eingehen auf die Maßnahmen zur Verbesserung des Leistungsfaktors.
Maßnahmen zur Verbesserung des OEE Leistungsfaktors
Die Verbesserung des Leistungsfaktors ist meist eine Kombination aus technischer Wartung, gezielter Schulung des Personals und Prozessoptimierung erfordert. Durch präventive und prädiktive Wartungsstrategien wird sichergestellt, dass die Maschinen stets betriebsbereit und effizient sind.
Die kontinuierliche Weiterbildung des Personals stellt sicher, dass die Bediener in der Lage sind, die Maschinen optimal zu nutzen. Schließlich sorgt die Prozessoptimierung dafür, dass die Produktionsabläufe reibungslos und ohne Verzögerungen ablaufen. All diese Maßnahmen tragen gemeinsam dazu bei, den Leistungsfaktor zu verbessern und die Gesamtproduktivität zu steigern.
Mit einem auf Overall Equipment Effectiveness (OEE) und weitere „Produktionskennzahlen“ spezialisierten SaaS-Tool können Unternehmen schnell, einfach und kosteneffizient detaillierte Einblicke in die Verfügbarkeit, Leistung und Qualitätsausbringung ihrer Anlagen und Maschinen gewinnen.
Die sich daraus ergebenden Kennzahlen werden für die systematische und kontinuierliche Optimierung genutzt. Der Nutzen und die erzielte Kosteneinsparungen jeder Maßnahme werden sofort sichtbar.
3. OEE - Qualitätsfaktor
Definition und Formel sowie die Ermittlung des OEE Qualitätsfaktors in der Praxis
Der Qualitätsfaktor ist die dritte Hauptkomponente der Gesamtanlageneffektivität (Overall Equipment Effectiveness, OEE). Er misst den Anteil der produzierten Einheiten, die den Qualitätsstandards entsprechen, an der Gesamtzahl der produzierten Einheiten.
Der OEE Qualitätsfaktor gibt an, wie effizient eine Anlage in Bezug auf die Produktion von einwandfreien Produkten arbeitet. Die Formel zur Berechnung des Qualitätsfaktors lautet:
Dabei haben die Qualitäts-Variablen folgende Bedeutung:
-
Anzahl der guten Einheiten
Die Anzahl der produzierten Einheiten, die den Qualitätsanforderungen entsprechen und keine Nacharbeit oder Ausschuss erfordern. -
Gesamtanzahl der produzierten Einheiten
Die gesamte Anzahl der produzierten Einheiten, einschließlich der fehlerhaften Einheiten.
In der Praxis streben Unternehmen danach, einen möglichst hohen Qualitätsfaktor zu erreichen, idealerweise nahe 100 %, was bedeutet, dass fast alle produzierten Einheiten den Qualitätsstandards entsprechen.
Ein typischer Qualitätsfaktor in einer gut kontrollierten und stabilen Produktionsumgebung könnte zwischen 90 % und 99 % liegen. In weniger optimierten Umgebungen oder bei sehr komplexen Produktionsprozessen kann der Qualitätsfaktor jedoch deutlich niedriger sein.
Beispiel zur Berechnung des OEE Qualitätsfaktors
In der Praxis wird die Anzahl der Gutteile oft dadurch bestimmt, dass im Betrachtungszeitraum von der bekannten Anzahl der produzierten Teile einfach die Anzahl Ausschuss- und Nacharbeitsteile abgezogen wird.
Insgesamt produzierte Teile = Gutteile + Ausschussteile + Nacharbeitsteile
Strategie zur OEE Optimierung der Qualität
Wie beim Thema der Verfügbarkeit und Leistung einer Anlage gilt auch bei der Qualität, dass Sie automatisiert und systematisch den IST-Zustand der Qualität Ihrer Anlagen und Maschinen erfassen sollten. Dies gelingt - wie mehrfach bereits erwähnt - schnell, einfach und kosteneffizient durch den Einsatz eines auf Produktionskennzahlen spezialisierten Software-as-a-Service (SaaS) Tools.
Es ist offensichtlich, dass fehlerhafte Teile einen großen Einfluss auf die Kosten und auf die Termintreue der Produktion haben. Je früher Produktionsfehler im Wertschöpfungsprozess festgestellt werden, umso geringer ist der entstehende Schaden.
OEE Formel - Berechnung der Kennzahl
Nachdem uns jetzt alle Overall Equipment Effectiveness (OEE) Faktoren bekannt sind, können wir abschließend die OEE Kennzahl recht einfach und korrekt berechnen:
OEE Betrachtungszeitraum
Physisch sind Ihre Anlagen rund im die Uhr (= 24/7) in der Produktion verfügbar, d.h. könnten theoretisch permanent und durchgängig genutzt werden. In der Praxis ergeben sich aber geplante Verluste durch Werksferien, Pausen, keine Aufträge und geplante Stillstände, d.h.
- Geplante Nicht-Produktion
- Geplante Stillstände
Diese „Verluste“ werden bei der Kennzahl "Totale effektive Anlagenproduktivität" (englisch: Total Effective Equipment Performance, TEEP) berücksichtigt, nicht aber bei der OEE Kennzahl. Hier werden ausschließlich die Verluste während der geplanten Produktionszeit betrachtet!
Geplante Produktionszeit
Die geplante Produktionszeit ist die Summe aller Zeiträume, in denen Ihre Anlagen für die tatsächliche Produktion eingeplant und verfügbar sind, abzüglich der geplanten Nicht-Produktionszeiten. Bei der Berechnung der OEE (Overall Equipment Effectiveness) werden nur die Verluste betrachtet, die während dieser geplanten Produktionszeit auftreten, wie z.B. ungeplante Ausfälle, reduzierte Geschwindigkeiten oder Qualitätsprobleme.
Die geplante Produktionszeit ist eine realistische Darstellung der tatsächlichen Verfügbarkeit Ihrer Anlagen für die Produktion, unter Berücksichtigung aller notwendigen und geplanten Unterbrechungen. Dies ermöglicht eine genauere und relevantere Bewertung der tatsächlichen Effizienz und Produktivität Ihrer Produktion.
OEE Fazit
Steigerung der Fertigungsproduktivität
In der modernen Fertigungsindustrie ist die Steigerung der Produktivität von zentraler Bedeutung, um wettbewerbsfähig zu bleiben. Durch die Implementierung fortschrittlicher Fertigungstechnologien und Automatisierungslösungen können Unternehmen ihre Produktionsprozesse optimieren und die Effizienz erheblich steigern.
Die Integration von OEE in die Prinzipien der Industrie 4.0 ermöglicht eine datengetriebene Optimierung der Produktionsprozesse durch Echtzeitüberwachung und vernetzte Systeme.
Exklusives Whitepaper
Lernen Sie die modernsten Ansätze der Industrie 4.0, die Sie in Ihrer Produktion schon morgen umsetzen können, um innerhalb von 4 Wochen Ihre Kosten um gut 20% zu reduzieren.
mehr erfahren