Manufacturing Execution Systems (MES): The Complete Guide [2025]
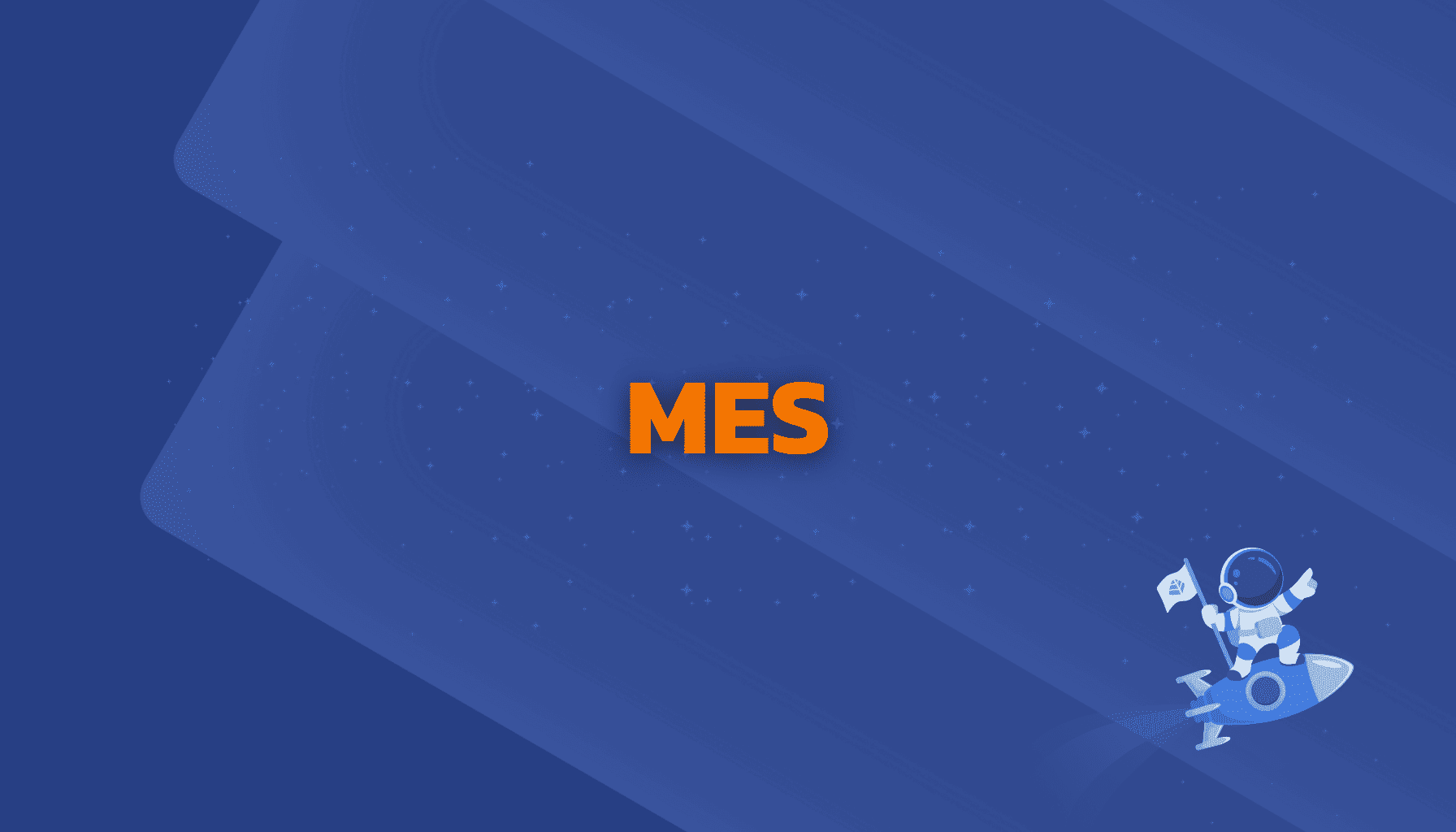
In this comprehensive guide to manufacturing execution systems (MES) and manufacturing operations management, you'll discover how modern MES solutions transform production operations and drive operational efficiency.
Learn how these advanced software solutions optimize the entire production process, from raw materials handling to finished product delivery, while ensuring seamless supply chain management integration.
What is a Manufacturing Execution System (MES)?
A Manufacturing Execution System (MES) is an advanced software solution that monitors, documents, controls, and optimizes the entire production process in manufacturing facilities. From plant floor operations to enterprise resource planning integration, MES software enables comprehensive production efficiency and operational efficiency improvements. Manufacturing companies significantly enhance their manufacturing efficiency and product quality through MES implementation, which enables seamless integration of production processes and maintenance management.
The system operates across the factory floor, coordinating production operations, resource allocation, and equipment utilization while maintaining regulatory compliance. Production departments, maintenance teams, and quality control units utilize MES for optimal resource utilization and production schedule management.
Mobile MES & Real-time Data Access between Operations Technology and Information Technology
Modern MES applications for smartphones particularly enable management to access critical real-time production performance data. As a functional layer between plant floor equipment (Operations Technology level) and enterprise resource planning systems (Information Technology level), MES software provides decision-makers with essential data needed for:
- Real-time production schedule monitoring
- Equipment utilization tracking
- Resource allocation optimization
- Supply chain management decisions
- Maintenance management planning
- Quality control verification
- Production operations oversight
- Manufacturing efficiency
- Production performance
- Equipment utilization
- Quality control systems
- Supply chain optimization
- Resource allocation
- Maintenance management
- Regulatory compliance
Legal Compliance & Term Definitions in MES Context
Modern manufacturing execution systems must address regulatory compliance requirements that demand complete documentation of the production process - especially for regulated industries and medical devices. While some may incorrectly apply the term MES to basic functionalities like Production Data Collection (PDC) or Machine Data Collection, a true manufacturing execution system encompasses comprehensive production operations management.
Types of MES Architectures
Modern manufacturing execution system architectures have evolved beyond traditional control systems to incorporate supply chain management and advanced production cycle optimization. The market for MES solutions continues to expand as manufacturing facilities seek to improve production efficiency and maximize operational efficiency through various deployment options.
According to recent market analysis, the global manufacturing execution system market is projected to reach $39.67 billion by 2029, driven by increasing demand for:
- Efficient production operations
- Enhanced equipment utilization
- Integrated maintenance management
- Optimized resource allocation
- Advanced quality control systems
In practice, three primary MES hosting architectures exist:
On-premises MES
Traditional client/server systems installed within the manufacturing facility's data center, offering direct control over production operations and equipment utilization.
Cloud-hosted MES (Lift and shift MES)
Traditional MES functionality hosted on external cloud infrastructure, enabling broader access to production performance data and maintenance management capabilities.
Cloud-native MES
The most advanced MES architecture, specifically designed for cloud environments using microservices to enable flexible production operations, resource allocation, and supply chain management.
MES as Software-as-a-Service from the Cloud
Cloud-native manufacturing execution systems offer significant advantages through Software-as-a-Service (SaaS) delivery:
- Immediate availability
- Scalable production operations
- Flexible resource allocation
- Cost-effective subscription model
- Enhanced supply chain integration
- Improved maintenance management
- Real-time equipment utilization monitoring
Traditional on-premises and cloud-hosted MES solutions typically require substantial initial investment (CAPEX) plus ongoing operational costs. Implementation timelines often extend several months before production operations begin.
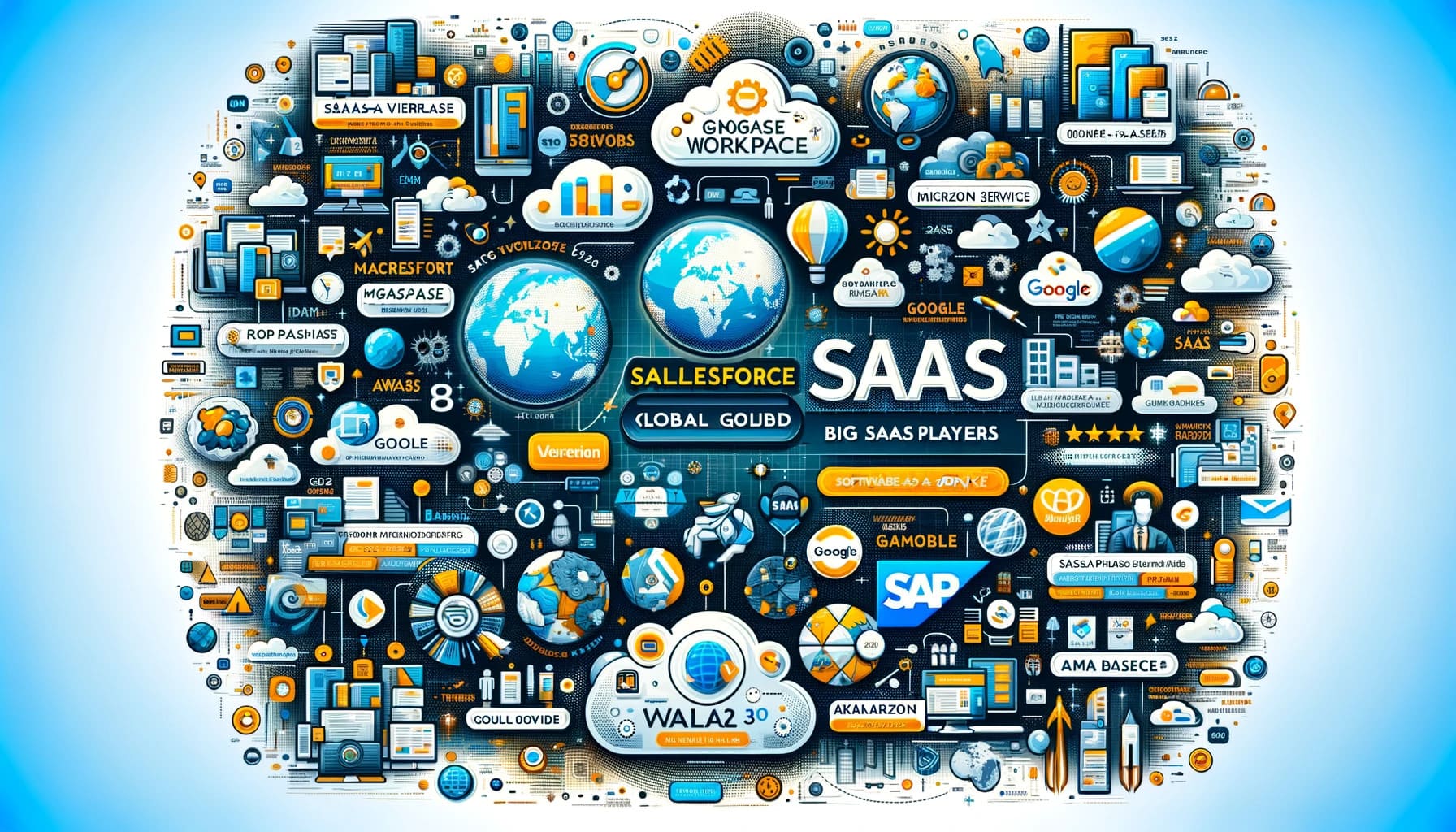
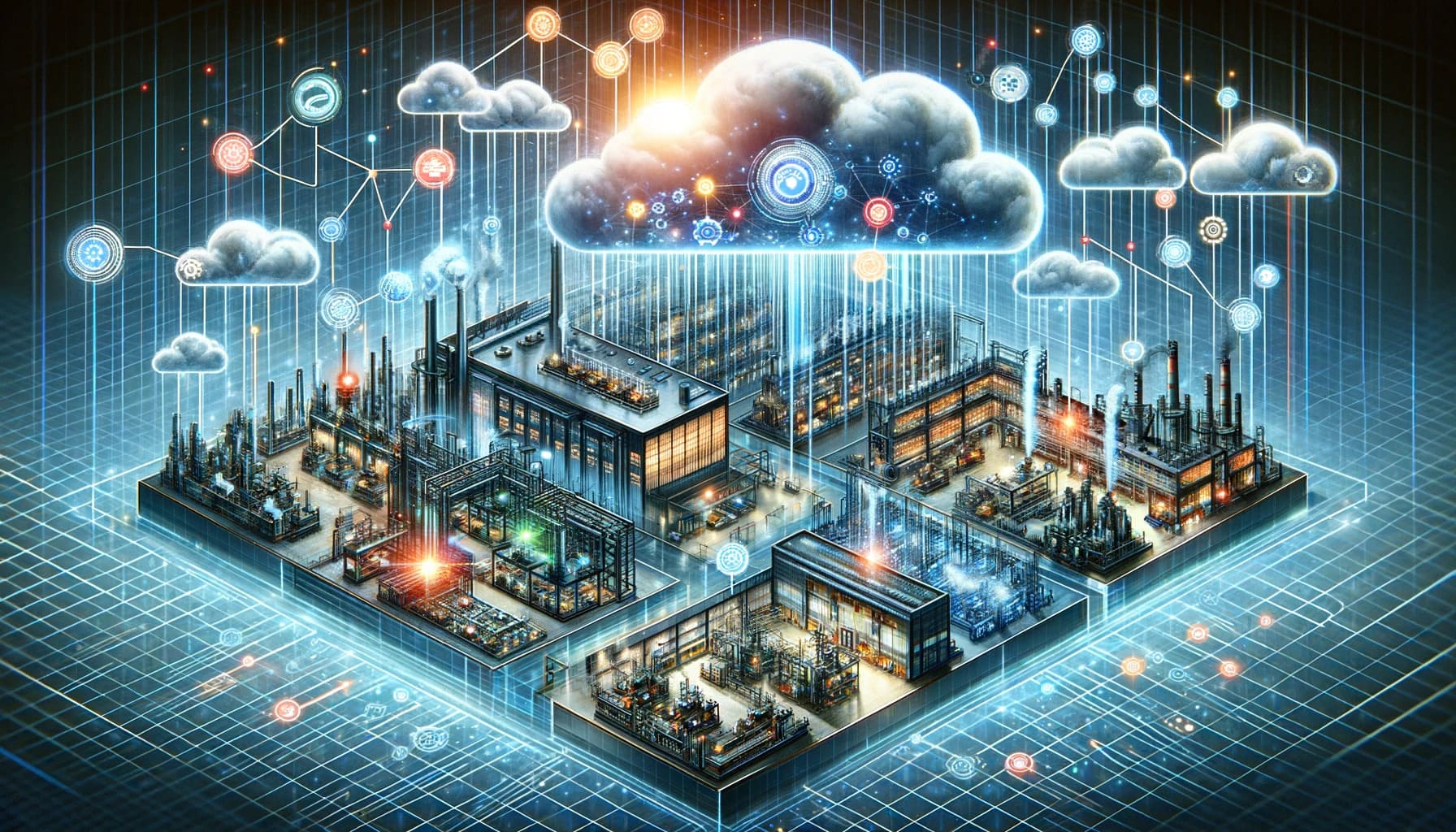
Cloud-native MES - evolution and paradigm shift
Discover how MES increases production efficiency, provides real-time data and integrates Industry 4.0 in your company. Optimize now!
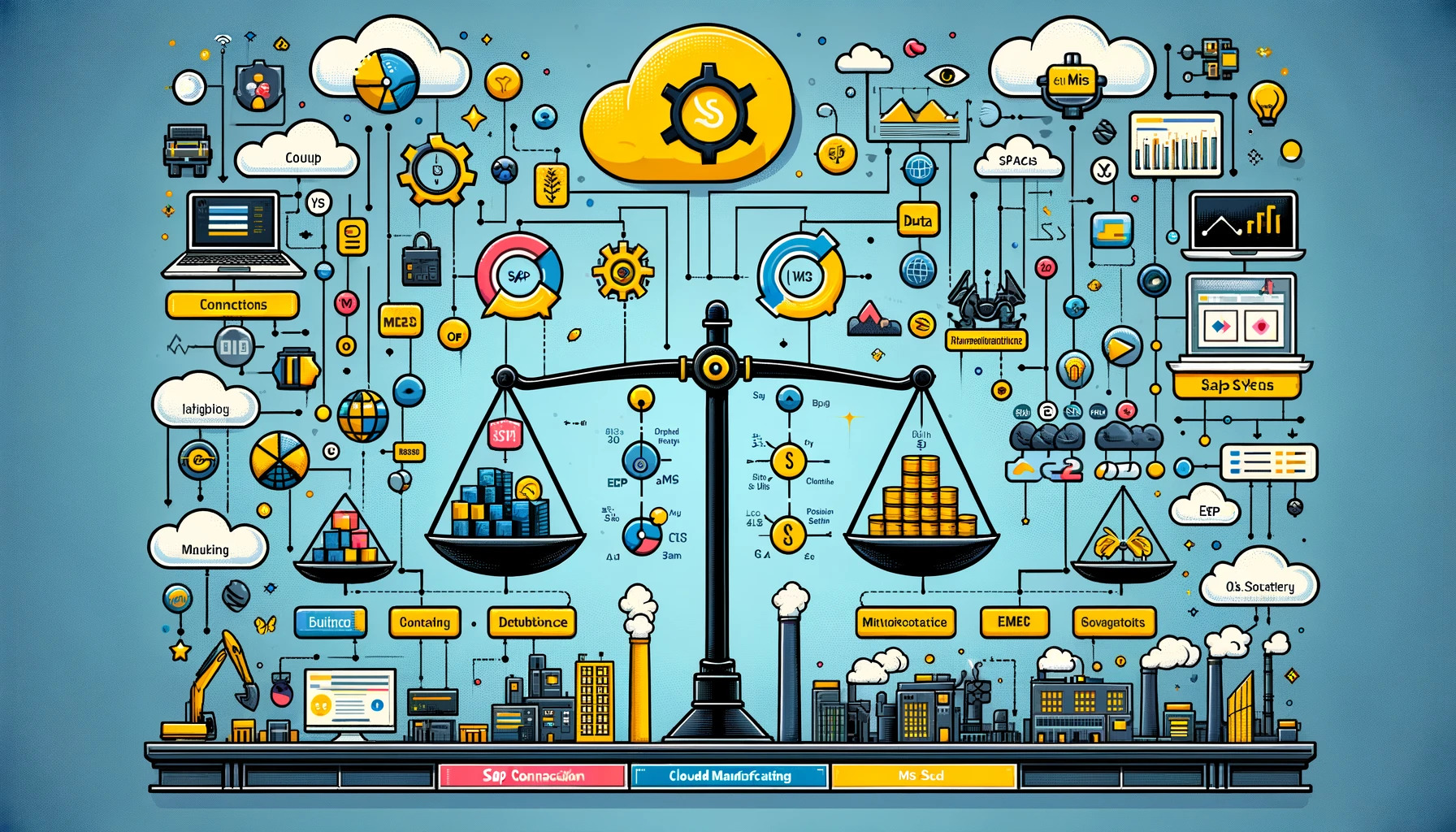
SAP DMC vs. Cloud-native MES Alternative
SAP MES vs. best-of-breed MES - SAP DMC compared to cloud-native MES alternatives. Find out more now.
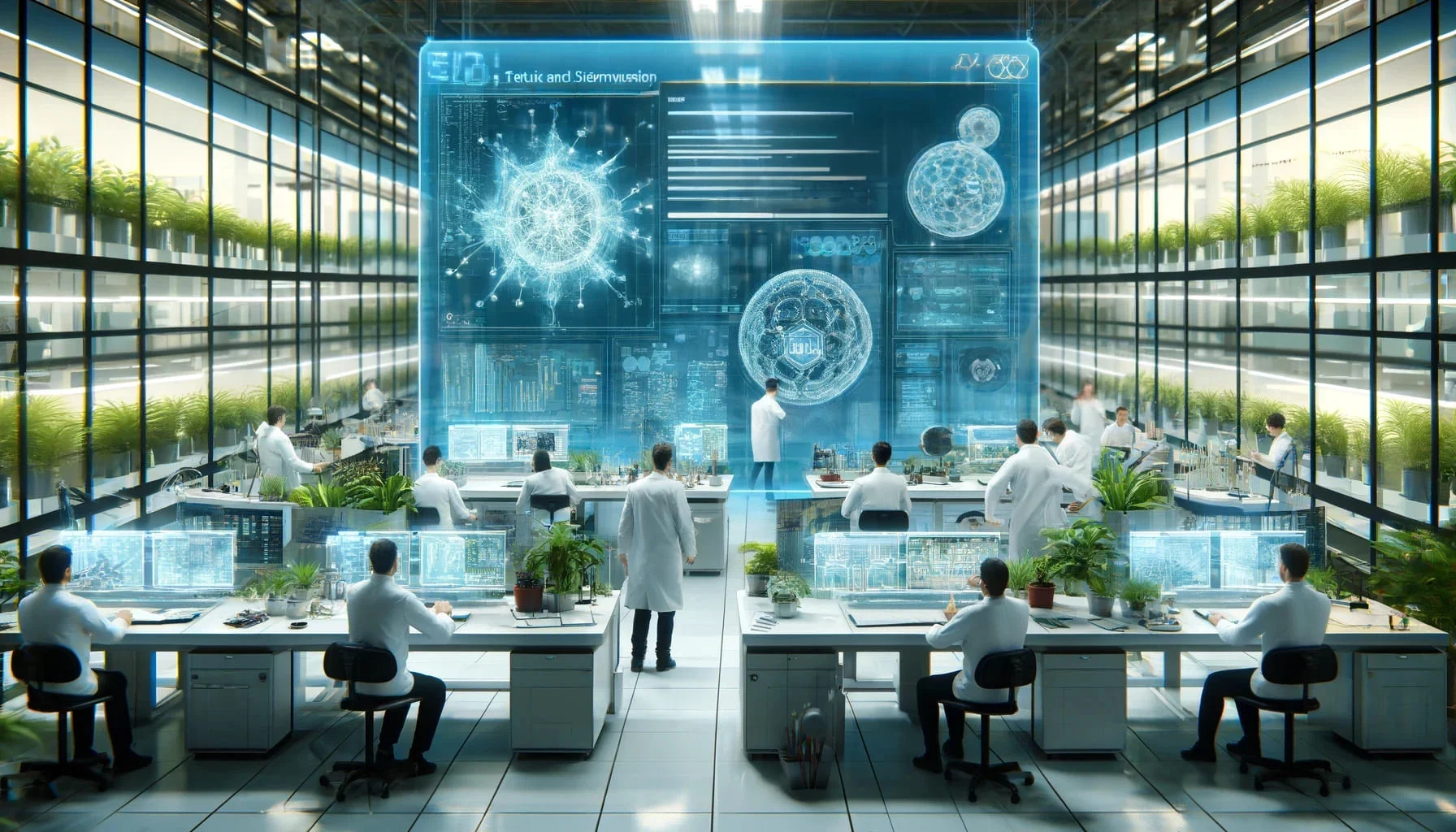
MES and Cyber security
Discover how cloud-native MES solutions are revolutionizing cyber security in the manufacturing industry. Optimize now!
What are the Main Benefits of an MES?
Manufacturing execution systems deliver comprehensive benefits across the entire production process, from raw materials management to finished product delivery. The relevance of each benefit varies by industry, process type, and specific manufacturing operations requirements.
Transparency to Increase Production Performance
Through real-time monitoring and analysis, MES solutions help optimize:
- Production efficiency
- Equipment utilization
- Resource allocation
- Quality control processes
- Overall Equipment Effectiveness (OEE)
- Maintenance management
- Supply chain operations
The system automatically collects and analyzes performance data, availability metrics, quality indicators, and process values in real-time. OEE serves as a critical production performance metric, combining availability, performance, and quality factors to reveal optimization opportunities across manufacturing operations.
Improved Decision Making
MES provides comprehensive production operations data and analysis, enabling informed decisions about:
- Resource allocation
- Equipment utilization
- Maintenance management
- Production schedule adjustments
- Supply chain optimization
- Quality control measures
- Regulatory compliance
Quality Improvement
Modern manufacturing execution systems enable quality improvements through:
- Real-time quality control monitoring
- Digital error tracking
- Production performance analysis
- Resource allocation optimization
- Equipment utilization data
- Maintenance management integration
- Supply chain validation
Advanced quality control capabilities help prevent sequential or mass errors while reducing costly recalls and waste. Resource utilization improves through active traceability and integrated maintenance management.
Inventory Control and Optimization
MES solutions enhance inventory control through:
- Automated ERP notifications
- Real-time production tracking
- Resource allocation updates
- Supply chain integration
- Raw materials management
- Work in Process (WIP) optimization
- Equipment utilization data
This comprehensive approach enables better management of manufacturing, transport, and storage operations while reducing manual inventory monitoring requirements.
Efficiency Increase through Paperless Production
Digital worker guidance systems provide:
- Electronic production orders
- Real-time operation updates
- Resource allocation instructions
- Equipment utilization status
- Maintenance management alerts
- Quality control procedures
- Production schedule updates
Compliance Requirements, Traceability, and Tracking
MES maintains detailed digital records including:
- Processing times
- Equipment utilization data
- Quality control metrics
- Resource allocation history
- Maintenance management logs
- Production performance analysis
- Regulatory compliance documentation
What are the Core Functions of an MES?
Modern manufacturing execution systems integrate essential functions spanning plant floor operations to enterprise resource planning integration. Based on VDI Guideline VDI-5600, seven core functions enable optimal production operations:
Detailed Planning and Control
- Production schedule optimization
- Resource allocation management
- Equipment utilization monitoring
- Supply chain coordination
- Quality control integration
Resource Management
- Equipment utilization tracking
- Maintenance management planning
- Resource allocation optimization
- Production performance monitoring
- Operational efficiency improvement
Material Management
- Raw materials tracking
- Supply chain integration
- Inventory control
- WIP management
- Resource utilization optimization
Personnel Management
- Resource allocation
- Skill qualification tracking
- Production schedule coordination
- Training management
- Performance monitoring
Data Collection
- Real-time production monitoring
- Equipment utilization tracking
- Quality control metrics
- Maintenance management data
- Resource allocation analytics
Quality Management
- Product quality control
- Process monitoring
- Resource utilization analysis
- Equipment performance tracking
- Regulatory compliance verification
Information Management
- Production performance analytics
- Resource allocation optimization
- Supply chain coordination
- Maintenance management integration
- Operational efficiency monitoring
MES Systems and ERP Systems as an Indispensable Duo
Modern manufacturing operations require seamless integration between MES and Enterprise Resource Planning (ERP) systems. While MES controls production operations with corresponding manufacturing data, ERP manages broader business planning. Together, they create a comprehensive ecosystem enabling:
- Production performance optimization
- Resource allocation management
- Supply chain integration
- Quality control monitoring
- Maintenance management coordination
- Regulatory compliance tracking
- Operational efficiency improvement
Interfaces and System Levels
ISA 95 defines the interfaces between Operations Technology (OT) and Information Technology (IT) in the MES environment:
Level 4 - ERP: Business planning and logistics Level 3 - MES: Manufacturing operations management Level 2 - Process control systems: Batch control Level 1 - Process control systems: Continuous control Level 0 - Process control systems: Discrete control
Modern Technologies and Trends
Contemporary manufacturing execution systems incorporate advanced technologies for improved production operations and operational efficiency. Key innovations include:
- Industrial Internet of Things (IIoT) integration
- Real-time production performance analytics
- Advanced equipment utilization monitoring
- Predictive maintenance management
- Integrated supply chain optimization
- Enhanced resource allocation systems
- Smart factory automation
- Production schedule optimization
Modern Technologies and Trends
Modern MES solutions build on advanced cloud technologies, enabling service-oriented integration with other systems. When selecting an MES, ensure it supports:
- Shop floor management functions
- Production operations control
- Equipment utilization monitoring
- Resource allocation optimization
- Quality control integration
- Maintenance management
- Supply chain coordination
Advanced analytics, data streaming, and artificial intelligence capabilities merge with MES data and services to create modern smart factory foundations. These systems, often called Manufacturing or IIoT platforms, offer:
- Vendor independence
- Third-party system integration
- Legacy system compatibility
- Enhanced operational efficiency
- Improved production performance
- Optimized resource utilization
How to Achieve a Smooth MES Implementation?
Successful MES implementation requires careful planning and execution to maximize benefits and minimize risks. Key recommendations include:
Clear Definition of Goals and Requirements
- Identify specific production operations needs
- Define quality control requirements
- Establish resource allocation priorities
- Set operational efficiency targets
- Plan maintenance management integration
Stakeholder Involvement
- Engage production management
- Include quality control teams
- Involve maintenance personnel
- Consult supply chain managers
- Designate MES key users
MES Architecture Decision
- Evaluate deployment options
- Consider scalability requirements
- Assess integration needs
- Review resource allocation demands
- Plan maintenance management approach
Market and Provider Evaluation
- Research available solutions
- Assess vendor capabilities
- Review integration options
- Evaluate support services
- Consider future scalability
Implementation Strategy
- Plan phased deployment
- Test system integration
- Verify production operations
- Confirm resource allocation
- Validate quality control
- Check maintenance management
Training and Change Management
- Develop training programs
- Create standard procedures
- Establish support systems
- Monitor system adoption
- Track operational efficiency
Data Management and Integration
- Define data requirements
- Plan system integration
- Establish security protocols
- Monitor data quality
- Ensure regulatory compliance
Continuous Improvement
- Track production performance
- Monitor equipment utilization
- Optimize resource allocation
- Enhance quality control
- Improve maintenance management
Following these recommendations helps ensure successful MES implementation, leading to improved production operations and enhanced operational efficiency. Contact our experts for personalized guidance on implementing modern MES solutions in your manufacturing facility.
Conclusion: The Future of Manufacturing Execution Systems
Manufacturing execution system (MES) solutions have become essential for modern manufacturing operations and business processes. As explored in this guide, MES software delivers comprehensive production process control while enabling efficient production operations across the shop floor.
Modern manufacturing execution systems excel in:
- Optimizing production performance and equipment utilization
- Enhancing process control and resource allocation
- Integrating enterprise and control systems
- Supporting production activities and labor management
- Improving inventory accuracy and maintenance costs
- Enabling informed business decisions through data analysis
The future of manufacturing operations continues to evolve with advances in industrial internet technologies. For manufacturing companies seeking to improve operational efficiency, implementing a modern MES solution is crucial for maintaining competitive advantage in today's digital world.
Contact our experts to learn how our manufacturing data and manufacturing execution systems can transform your production processes.