Lean Production
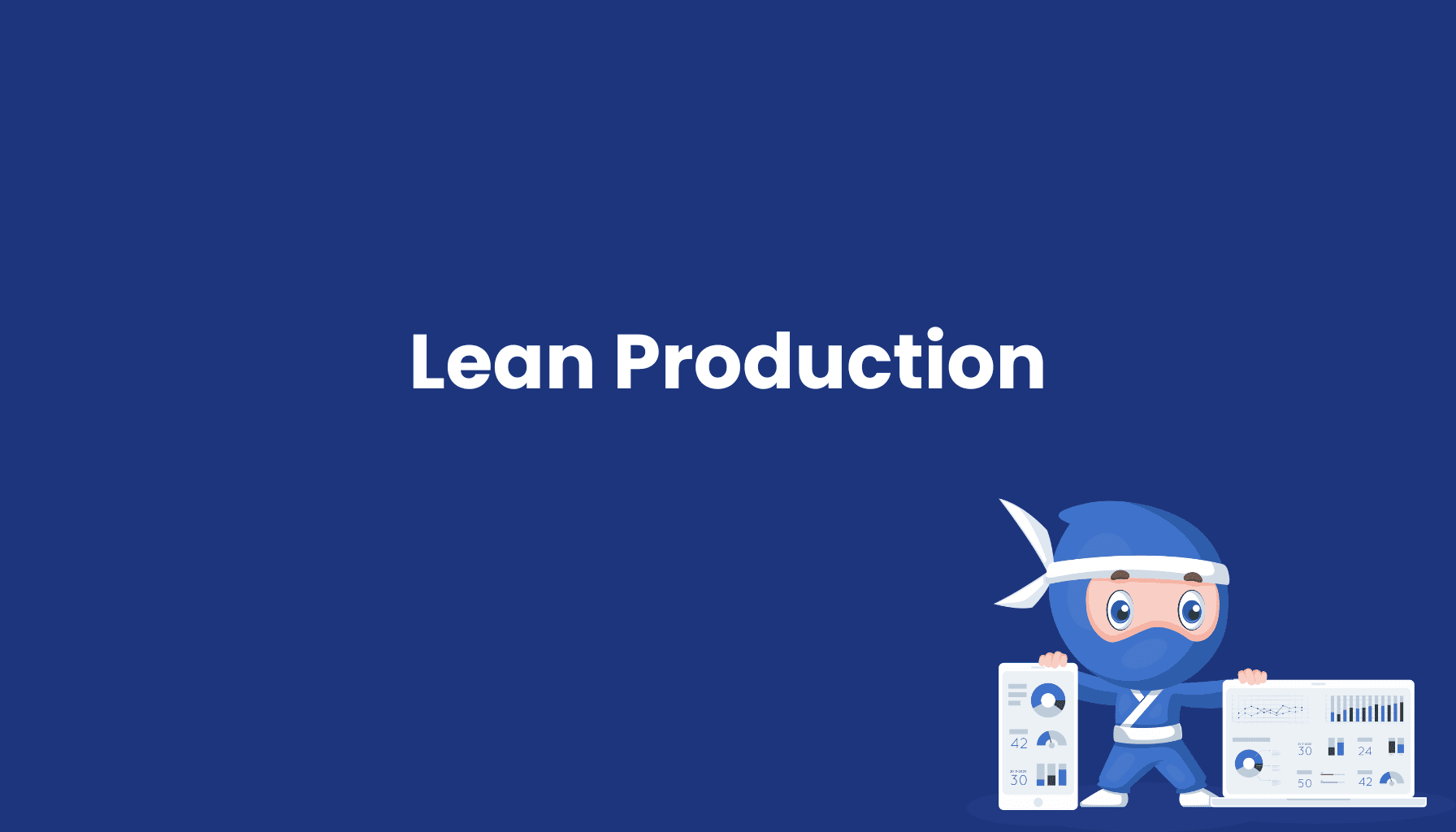
What is Lean Production?
Lean Production, also known as Lean Manufacturing, is a management philosophy that aims to maximize customer value by minimizing waste within manufacturing processes. Originally developed in the Japanese automotive industry, particularly at Toyota, Lean Production has become a standard practice in various industries. The primary goal is to increase efficiency, reduce costs, and simultaneously improve quality and flexibility in production processes.
Key Elements of Lean Production
-
Value Creation and Waste Elimination: The core focus of Lean Production is identifying and eliminating waste (muda). Common types of waste include overproduction, waiting times, unnecessary transportation, over-processing, excess inventory, unnecessary movement, and defects. By concentrating on value-added activities, processes become leaner and more efficient.
-
Continuous Improvement (Kaizen): Kaizen is a fundamental component of Lean Production. It involves the ongoing pursuit of small, incremental improvements in work processes. All employees, from management to the shop floor, are encouraged to contribute suggestions for improvement, which helps to continuously enhance efficiency and quality.
-
Just-In-Time (JIT) Production: JIT aims to produce only what is needed, when it is needed, and in the required quantity. This method helps minimize inventory levels and increases production flexibility. It requires precise planning and reliable suppliers to function effectively.
-
Quality Management: Quality is integral to Lean Production. Continuous monitoring and immediate corrective actions ensure that products meet high-quality standards. Techniques such as "jidoka" (automation with a human touch) and "poka-yoke" (mistake-proofing) help prevent errors and maintain product quality.
-
Flexibility and Adaptability: Lean systems are designed to be flexible and adaptable, enabling companies to respond quickly to changes in the market or customer demands, thus enhancing their competitiveness.
Benefits of Lean Production
- Cost Reduction: By eliminating waste and optimizing processes, operational costs are reduced.
- Improved Quality: Continuous improvement measures and strict quality controls enhance product quality, leading to higher customer satisfaction.
- Increased Efficiency: Lean methods streamline production processes, reduce cycle times, and improve resource utilization.
- Greater Customer Value: By focusing on value-adding activities, Lean Production ensures better service to customers, increasing the perceived value of products and services.
Lean Production in Industry 4.0
In the era of Industry 4.0, Lean Production integrates modern technologies such as IoT, Big Data, and artificial intelligence to enable more precise and efficient production processes. These technologies help companies monitor and optimize their production systems in real-time, leading to further efficiency gains and cost reductions.
Read our detailed blog post on Lean Production Essentials: Basics and the 8 main wastes here.